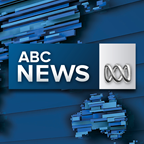
Posted

In the centre of the Maylands peninsula, surrounded by lakes, a golf course and houses, sits a monument to the heavy industry that once dominated the area.
The Maylands Brickworks closed more than 30 years ago, but the red brick Hoffman kiln and other parts of the operation still sit tall, preserved behind protective fencing.
There is now talk of finding a new use for the historical site and of letting the public explore a largely forgotten part of the city's heritage.

When the brickworks were established in 1927 the area was largely undeveloped; the landscape was dominated by farmland and the newly created Maylands Aerodrome.
"The person that developed the brickworks was Robert Law and he had a partner, Mr King Atkins, and they were doing lots of building work around WA," Penny O'Connor from the State Heritage Office said.
"They had set up brickworks in Helena Vale and then Law struck gold, metaphorically, in that he found these clay deposits on the Maylands peninsula.
"There is this big deep bend in the river and the clay had built up.
"It made sense to build the kilns and do all the processing work right where the clay was.
"Obviously it was also really close to the city where a lot of building works were going on anyway."

A huge amount of excavation and construction took place, forming two large clay pits (now the Maylands lakes), two large Hoffman kilns (one was damaged by the Meckering earthquake in 1968 and demolished) and an array of drying sheds for the bricks.
"Looking at aerial photography from the '50s until the '80s, it was phenomenal the level of excavation work that was going on, because they were actually mining the clay from the Maylands peninsula and pushing it straight through into the brickworks," Dr O'Connor said.
"It is quite hard to imagine now."

The clay went first into the pug mill, a processor in a large wooden and corrugated iron building that refined the clay and mixed it with water into a fine paste. That clay mix was then fed into the brick extruder.
From there, the extruded bricks were cut and laid in vast drying sheds. Today, just one of these structures remains.

After drying out they went into the kilns.
"It would have been pretty noxious," Dr O'Connor said.
"The way that they fired the bricks was to use powdered coal.
"They loaded up the kiln with all the bricks that had been dried over time; they were hard but weren't fired.
"Then they would pour in powdered coal onto the bricks and that was what would fire them.
"So the powdered coal would be raining down between the gaps in the bricks.
"It wasn't a part of town where people lived; it was very industrial, and as a peninsula it could kind of be isolated from the rest of the suburbs."

The brickworks operated for almost 50 years before closing in 1983.
"By the end it was very highly automated and considered one of the most advanced factories in the whole of Australia," Dr O'Connor said.
There were initial plans to demolish the brickworks and fill in the clay pits, but community opposition at the time saw the site preserved.
"Even at the time that it closed the site was valued," Dr O'Connor said.
"There were proposals to fill in the lakes and there was public outcry about that and they were turned into manmade lakes."

The brickworks site is now fenced off from the public, while the surrounding area has been developed for housing.
"There has been a lot of development go on around them, but these types of engineering buildings were built to last and they have stood the test of time since they have been decommissioned," Dr O'Connor said.
Thirty-four years after the closure, the local council and the State Heritage Office are looking at how the site might be reactivated and adapted for reuse.
Graeme Gammie from the Department of Planning, Lands and Heritage said community consultation would start early next year and that all interested members of the public would be encouraged to have their say.
"Several options have been explored as possible compatible new uses for the site and will be shared with the community for discussion," he said.
"However, residents and stakeholders are encouraged to raise other adaptive reuse options that might be economically and socially feasible while respecting the heritage values of the place."
Topics: history, industrial-design, local-government, architecture, human-interest, maylands-6051, perth-6000