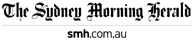
The lofty ambitions of two former Fortescue executives, who want to build a $US2.1 billion ($3.2 billion) green iron ore processing plant in the Pilbara within five years, will require a gigantic infusion of money.
Michael Masterman and Bart Kolodziejczyk formed Element Zero at the end of 2022, which aims to reduce the carbon footprint of iron ore, Australia’s most lucrative export industry. It’s a big step up from the $US10 million the group raised at the start of this year in seed funding, and there are plans to undertake another capital raising later in the year, targeting $US50 million to $US100 million.
Iron is the key ingredient in steel production, which the world depends on for construction and manufacturing. However, production of iron and steel emits a combined 3.4 billion tonnes of carbon annually, or 7 per cent of global emissions, according to energy analysts Wood Mackenzie.
If the international agreement to limit global warming is to be achieved, emissions must reach net-zero by 2050. To decarbonise the iron ore and steel industries, Wood Mackenzie has estimated it would require a mind-bending $US1.4 trillion in global investment – almost equivalent to Australia’s total annual gross domestic product.
Former Fortescue executives Bart Kolodziejczyk (left) and Michael Masterman want to build a $3.2 billion green iron ore processing plant in the Pilbara within five years. Credit: Eamon Gallagher
This makes the capital needs of Element Zero seem less of a tall order.
“There is so much interest in what we do both in Australia and globally, in particular in the US, that we believe that we can make it,” said Kolodziejczyk, Element Zero’s co-founder and chief technology officer.
Element Zero, which employs about two dozen staff, has developed and patented a technology to reduce iron ore to pure iron through an electrochemical process.
An alkaline solution and electric current are used to separate pure iron from silica, alumina and oxygen. Iron ore is dissolved into the solution and when electricity – from a renewable source – passes through it, the pure iron collects on a cathode.
The group said it had also made progress on decarbonising silicon.
Element Zero has pitched itself to investors as a platform company, its technology aimed at converting metal ores to metals, not only iron ore, with zero carbon emissions.
About 560 million tonnes of iron ore are shipped through Port Hedland annually.Credit: Ian Waldie
Element Zero is seeking West Australian government approval for its green iron processing plant on 25 hectares in the Boodarie strategic industrial estate near Port Hedland. Kolodziejczyk said the group was also seeking a separate site to build a wind and solar farm to power the plant.
He said within five years, the plant could process 5 million tonnes of iron ore feed into 2.7 million tonnes of green iron a year. There are plans to scale up to processing 50 million tonnes.
Element Zero’s pilot plant in Perth still a long way from industrial scale. It is processing 100 kg of iron ore daily, bought from major iron ore producers.
A process known as direct reduction uses natural gas, or methane, in a furnace to extract pure iron from iron ore. Some companies such as Fortescue have explored replacing methane with green hydrogen.
Loading
Kolodziejczyk, once Fortescue’s chief scientist, led a push to develop green hydrogen to decarbonise the company’s mining operations and shipping fleet.
Masterman, Element Zero’s chief executive, has had a long career in the energy industry, including in Europe and also worked as Fortescue Future Industries’ chief financial officer. He was chairman of renewable energy group Squadron Energy, part of the Tattarang group of companies, which are linked to Fortescue founder Andrew Forrest.
“The entire industry has enormous commercial pressures, shareholder pressures and goodwill to find technology solutions that can reduce the carbon emissions from converting iron ore into iron,” said Masterman. “We can significantly move the dial.”
About 560 million tonnes of iron ore are shipped through Port Hedland annually.
“If we can move to converting the vast, exceptional natural resources we have in Australia to metals, rather than just exporting the raw ore, that’s going to have two impacts. It’s going to help significantly reduce carbon emissions and ... substantially strengthen Australia.”
Element Zero faces strong competition from other companies that have or are developing technology to make green iron and steel, among them Fortescue Future Industries, which last year claimed it had built a pilot plant that could turn iron ore into green iron using a membrane.
Element Zero is exploring converting other metal ores to metals with zero carbon emissions, including lithium, nickel and silicon.
Kolodziejczyk acknowledges the challenges but remains confident, predicting that eventually some of the major iron ore producers, among them BHP, Rio Tinto, Fortescue, Vale, and Roy Hill, could become investors in Element Zero. “We believe that some of those majors will come and invest in us.”
Loading
Companies such as BHP and Vale have invested in clean tech groups such as Boston Metal, which is working on decarbonising steelmaking. BHP also has a stake in Electra, a start-up focused on decarbonising iron making.
In January, H2 Green Steel, which has technology that it says will help to decarbonise European steel, raised €4.2 billion ($6.9 billion) in debt financing. The start-up was founded in 2020.
Kolodziejczyk said Element Zero was also holding discussions with potential customers in Japan and South Korea for its green iron.
“Given how quickly we are moving with the technology scale-up, and also with the project in the Pilbara, we believe it’s a good time to secure those initial agreements,” he said. “That’s what we’re going to do in the next couple of months. We believe the first offtake will come from Japan. Obviously having those agreements in place will help us with the next fund raise.”
Masterman said Element Zero was providing potential customers with samples of its green iron so they “can test it to understand any adjustments they might need to make in their systems to be able to utilise it in their processing plants”.
Kolodziejczyk said Element Zero’s next fund raising could be as much as $US100 million. Masterman declined to provide a figure, saying instead the group was focused on proving its technology in stages to secure funding.
Element Zero is also exploring potential grants from the United States through the Inflation Reduction Act (IRA). The IRA has directed hundreds of billions of dollars to clean energy projects, including electric vehicles, to accelerate the country’s transition to net-zero.
Loading
The IRA has fuelled a manufacturing boom in the US but that rapid growth in cleantech manufacturing has come at a cost. It has driven a huge increase in electricity demand, as has the development of artificial intelligence and digital currencies, which threaten to slow the path to net-zero, as renewable energy companies struggle to keep pace.
The Future Made in Australia Act, the new industrial policy abbounced last week, was immediately dubbed a mini-version of the IRA, although details are yet to be released. It will target advanced manufacturing and clean energy projects with government-funded incentives.
The push to decarbonise the iron ore sector comes amid pressure on exports. Vivek Dhar, director of the Commonwealth Bank’s mining and energy commodities research team, has forecast that iron ore prices will average between $US100-$110 a tonne for the remainder of the year, after hitting $US140 in January.
He said there were risks the price could fall below those forecasts if growth slowed in China, as a result of a slump in its property sector. China imports almost 75 per cent of the world’s iron ore.
Element Zero is exploring converting other ores with zero carbon emissions, including lithium, nickel and silicon.
Kolodziejczyk said the group had made good progress with silicon. “We are trying to refine the process. The team is working towards that, and we believe that could be our second offering.”
Loading
Silicon is used in the manufacturing of solar cells and microchips. The US has also introduced the CHIPS and Science Act that aims to boost investment, manufacturing and research and development in semiconductors.
“If we’re able to take literally sand and convert it into silicon metal, with very little carbon emissions, that makes a major difference to the supply source of silicon metal and the carbon emissions that come from producing it,” said Masterman.
“Silicon is a very exciting one for us and one in which we might be able to move more quickly. We could accelerate parts of the silicon plant in parallel with the work we’re doing in iron ore. There are some significant opportunities in the United States we’re considering.”
The Business Briefing newsletter delivers major stories, exclusive coverage and expert opinion. Sign up to get it every weekday morning.