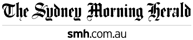
Ammonia production is a $US100 billion ($154 billion) global industry, and 70 per cent of that is for agriculture. The synthesis and transport of ammonia accounts for about 2 per cent of global emissions from both energy usage and the chemical process itself.
The true impact on greenhouse emissions is many times greater because once the fertiliser is applied to the soil, it releases nitrogen oxides – potent greenhouse gases that also cause smog and acid rain.
From left: PlasmaLeap co-founder Samantha Cullen, chief executive Frere Byrne and co-founder P.J. Cullen.Credit: Janie Barrett
There have been many attempts to create green ammonia, and one of the most promising is happening in Sydney’s inner west at the headquarters of PlasmaLeap.
The start-up, which grew out of University of Sydney and University of NSW research, claims it can make fertiliser out of renewable electricity, air and water at significantly lower cost and energy intensity than traditional methods. The technology can also be distributed and deployed on location.
The invention at PlasmaLeap, which enables the production of fertiliser with minimal carbon emissions.Credit: Janie Barrett
PlasmaLeap chief executive Frere Byrne says the researchers made a breakthrough discovery about two years ago and have been scaling it to something that could disrupt the entire fossil fuel-driven fertiliser market. It uses plasma, which is a “highly excited gas”, and occurs naturally in lightning.
“What we’re doing is replicating the process when lightning hits soil, which is a plasma-driven process that fixes nitrogen to the soil through electricity,” Byrne says.
“The technology captures very, very tiny lightning strikes – electrical discharges. We capture those discharges inside bubbles, the bubbles that are made of plasma, and then we proliferate them through liquids.”
In a nutshell, PlasmaLeap uses renewable electricity to make plasma and then employs the plasma to fix nitrogen and oxygen out of the air to make nitrates. In a second conversion, it can use plasma to turn the nitrate into ammonia, by replacing the oxygen with hydrogen.
For every kilogram of nitrogen put on a crop, the Haber-Bosch process generates the equivalent of just under 11 kilograms of carbon dioxide. The PlasmaLeap process, Byrne says, generates closer to 0.1 kilograms of carbon dioxide.
Graham Gall of Dawson River Pastoral Co. says the technology could offer greater self-reliance and sustainability for the agricultural industry.
“In Australia, almost all our nitrogen fertilisers are sourced from overseas, leaving us vulnerable to global supply chain disruptions and price fluctuations,” Gall says. “PlasmaLeap’s solution allows us to produce nitrogen on-farm using green energy sources, which is a game-changer.”
Building homes with hemp
Expect to hear a lot more about hemp as a building material since actor Zac Efron recently revealed he is using it to construct an eco-home in northern NSW near Tweed Heads.
“Hempcrete” – concrete made from hemp fibres – is not new. Archaeologists have confirmed it was used in a bridge in sixth century France, back when it was still Gaul. The Romans used hemp in the mortar for Hadrian’s Wall. It’s in buildings in South-East Asia that have stood for 1000 years. And it has been used in modern times for several decades, with a builder mixing a pallet of hemp and a pallet of binder on site and casting it in a frame.
Actor Zac Efron, pictured here on the red carpet in 2022, is building a home in northern NSW out of hempcrete.Credit: NNA / Kate Rafferty
X-Hemp founder and managing director Andi Lucas says the innovation is making prefabricated building materials from hemp.
“Commercial customers are coming to us, and they want us to be giving them [a] finished product,” Lucas says. “They want to have hemp blocks arriving on site. They want hemp timber substitutes arriving on site. They want hemp wall insulation arriving on site.”
The company is based in Tasmania, close to a supply of hemp from both agricultural waste and purpose-grown crops. Lucas is raising capital to expand nationally.
Lucas lost her home to a bushfire in Tasmania in 2013 and an apartment in Colorado to a flood later the same year. She was drawn to hempcrete because of its fire-retardant properties, became interested in its ability to sequester carbon, and started a business.
X-Hemp founder and managing director Andi Lucas became interested in hemp after losing two homes, one to a bushfire and one to a flood.Credit:
Lucas says a hectare of hemp should sequester about 15 tonnes of carbon through its growth cycle of about 120 days, and there are peer-reviewed studies that suggest a hempcrete building will continue sucking in carbon dioxide for several years after construction.
An average-sized hempcrete house will lock up 5.5 tonnes of carbon over the course of the building’s lifespan, she says, making it not just carbon-neutral but even carbon-negative if the hemp is locally grown.
So far, X-Hemp has supplied materials for 35 homes, plus a $131 million project with the University of Tasmania.
Hempcrete also has insulating properties to keep a house passively warm and cool, and anti-mould properties. Asked for the downside, Lucas admits it’s not the cheapest material, but she adds that you don’t have to be Zac Efron.
Hempcrete was used in the construction of a project for the University of Tasmania.Credit:
“We have solidly middle-class folks who are building houses that they’re planning to live in and that’s our client base,” Lucas says.
Brewing palm oil from yeast
When Thomas Collier was 21, his then-girlfriend and now-wife went to Borneo to work on a documentary about how the palm oil industry was fuelling deforestation and threatening orangutans and other wildlife.
“When she came back, she told me about all the things she saw first-hand, which were quite upsetting,” Collier says. “I couldn’t do too much about it at the time, but it stuck with me.”
Collier completed a PhD at Macquarie University that focused on how to sustainably produce palm oil, a common ingredient used in food and in 70 per cent of cosmetic products, including soaps. He also visited Borneo himself.
Synthetic biologist Tom Collier has invented a palm oil substitute using yeast.Credit: Janie Barrett
Rather than trying to improve plantations, Collier wanted to find a replacement that didn’t cause deforestation in the first place.
After years of research, he has cracked the goal of producing palm oil that is indistinguishable from that found in nature – only it doesn’t come from a palm tree, it is made by genetically modified yeast.
Collier has founded a company, Levur, and won backing from Main Sequence Ventures to focus on palm oil for the cosmetics industry.
Using a technique similar to brewing beer, Collier is feeding the yeast with sugar, though he hopes to move to compost to make it part of the circular economy. The yeast organisms are physically separated and removed, leaving behind an isolated oil.
Levur will focus initially on palm oil used in cosmetics. The picture shows the yeast growing, the oil, and moisturiser containing the oil.Credit: Janie Barrett
He would love for his technology to be used in the communities that produce palm oil to ensure a livelihood for people “just trying to put food on the table”.
Splitting solar between apartments
More than 4 million Australian households have rooftop solar, but most of the 2 million people living in apartments are missing out or only have it to power lights in common areas.
Melbourne-based Allume is trying to change that, with smart hardware called SolShare.
Mirvac’s Tullamore apartments in Doncaster, Melbourne with solar panels and Allume’s SolShare.Credit:
The company recently received a federal government grant of $3.77 million to help develop the technology, which has been installed in 4000 apartments in Australia, New Zealand, the United States and Britain so far.
Founder and chief executive Cameron Knox says SolShare can split solar between five and 60 dwellings, but the average size was about 12 purely because of the prevalence of older blocks of flats.
As the electricity is piped down from the solar system, it enters the SolShare box, an inverter power-sharing device that physically splits the energy and divides it between various dwellings. An algorithm dynamically decides where and when to send the energy, ensuring every apartment receives a fair share over a month.
Loading
“If we’re neighbours in an apartment building, and I switch on my kettle whilst you go out to walk the dog, SolShare will send me proportionally more of my solar allocation at that point in time than it will yourself,” Knox says.
“Then you might get home and switch your microwave on. At that point in time, you’ll be prioritised above me to catch back up.”
Knox says the NSW government will follow Victoria’s lead and introduce an incentive for solar on apartment buildings next year.